引文格式:
Y. Xu, R.Z. Wang, Y. S. Sato, et al. Interfacial characteristics and microstructural evolution of austenitic to ferritic stainless steels bimetallic structure fabricated by wire-arc directed energy deposition [J]. Additive Manufacturing, 2025, 98: 104629.
Yipu Xu, et al. "Interfacial characteristics and microstructural evolution of austenitic to ferritic stainless steels bimetallic structure fabricated by wire-arc directed energy deposition." Additive Manufacturing 98 (2025): 104629.
Y. Xu, R.Z. Wang, Y.S. Sato, S. Tokita, Y. Zhao, Z. Yi & A. Wu. (2025). Interfacial characteristics and microstructural evolution of austenitic to ferritic stainless steels bimetallic structure fabricated by wire-arc directed energy deposition. Additive Manufacturing, 98, 104629.
背景简介
在现代工业应用中,材料性能的空间变化设计使工程结构比单一金属材料更高效。其中,双金属结构的制造被认为是实现局部性能优化最有前景的方法之一。近年来,增材制造技术因其高精度、高效率和高灵活性,为双金属结构的制造提供了新机会。与传统异种金属焊接相比,增材制造技术显著减少了因后续加工带来的时间和材料成本。其中,基于电弧的送丝增材制造因其高沉积速率和能量密度而备受关注,但传统电弧增材工艺一次仅能引入一种丝材,难以高效制造双金属结构。为了解决这一问题,新型双丝电弧增材系统被开发出来,能够同时或顺序送入两种金属丝材,从而实现多材料结构的制造。基于双丝电弧增材的双金属结构制造仍面临界面区域缺陷和微观结构控制的挑战。界面区域的孔隙、裂纹等缺陷通常由材料的热膨胀系数差异或化学成分突变引起,而微观结构的演化则受到复杂热历史和元素扩散行为的耦合影响。当前研究多关注界面微观结构的形貌和整体构件性能,对于电弧增材制过程中非平衡凝固和元素扩散行为对界面微观结构演化的影响研究较少。本研究选择奥氏体不锈钢和铁素体不锈钢作为填料,通过基于钨极气体保护电弧焊的电弧增材系统制造双金属结构。系统性地开展了界面表征,包括微观结构观察、元素分布分析和机械性能评估。同时借助温度场模拟,深入研究了界面区域微观结构演化机制。本研究深入探讨了双金属结构的界面特性及其形成机制,为未来成分梯度设计和工艺参数优化提供了重要的理论指导。
成果介绍
(1)本研究制备了由304奥氏体不锈钢和430铁素体不锈钢组成的双金属结构,如图1a所示。与送丝相关的设备包括送丝机和双焊丝送料喷嘴,以及直径为1.2mm的ER304和ER430焊丝。六轴机械臂 (FUNUC M20iA) 连接到钨极惰性气体 (TIG) 焊枪以进行连续沉积。焊接电流校准为200A,电压保持在平均值17V,根据电流波动自动匹配。沉积过程中采用恒定的2m/min送丝速度和0.25m/min的焊枪移动速度。两根焊丝的交叉点与焊枪的距离保持在8mm处,送丝角度始终设置为30°。焊丝从熔池前沿进入,熔池由流速为15L/min的纯氩气保护。为了避免过多的热量积聚,层间冷却时间为60s。图1b为增材制造的双金属结构,其中多层双金属结构沉积在SUS304基板(250mm × 75mm × 10mm)上。首先,使用ER304焊丝沉积前10层。随后,在凝固的奥氏体不锈钢上沉积ER430焊丝以形成最上面10层。采用Z字形沉积模式以提高成形性,最终尺寸为200mm × 7mm × 20mm。随后,用电火花加工机沿构建方向从沉积态双金属结构中加工出金相样品和拉伸试样。前者的直接目的是进行界面表征,而后者的直接目的是评估力学性能。拉伸试样的详细尺寸如图1b所示,标距长度为5mm,标距宽度为2mm,厚度为1.2 mm。
.png)
图 1. (a) D-WAAM系统示意图;(b) 双金属结构的放大视图,以及制备的冶金样品和拉伸试样。
(2)显示了沉积态双金属结构的宏观概览、硬度分布和金相图像。从宏观概览来看,没有发现明显的缺陷,如孔隙和裂纹,如图2a所示。此外,界面区域在蚀刻后变色,因此双金属结构可粗略地分为四个不同的区域:R1、R2、R3和R4。四个区域的相关维氏硬度分布如图2b所示。界面区域的硬度明显高于R1和R4区域,其中最高值在R3中达到275 HV。因此,此处的界面区域可称为界面强化区 (ISR)。除ISR之外,硬度从底部到顶部呈降低趋势。图1c分别展示了通过光镜观察到的典型金相图像,其中R1和R4中的大柱状晶粒朝构建方向生长。R2中出现了一些块状和针状图案,而R3显示出完全的马氏体组织。
.png)
图2. (a) 沉积后样品截面的宏观概览,(b) 沿双金属构建方向的相关硬度分布,以及 (c) 每个区域放大后的金相形貌。
(3)鉴于图2b中从R4到R3观察到硬度迅速增加,因此进行EBSD测试以表征R3和R4之间界面的微观结构分布,如图3所示。基于相图,基体沿着构建方向从FCC相转变为BCC相。通过结合IQ图和KAM图,可以容易地推断出BCC基体对应于α'-马氏体,其特征是更高的灰度值和KAM值。有趣的是,即使距离R4较远,在R3内也可以识别出细小的γ-奥氏体。而细小的γ-奥氏体在R2内完全消失,让位于大面积的δ-铁素体区域,以白色箭头突出显示。应当注意,由于彼此的晶格参数相似,相图无法区分铁素体和马氏体相。
.png)
图3. 从R2至R4的界面微观结构分布。
(4)为了在纳米尺度下区分铁素体和马氏体相,R3的元素偏析情况由能量色散谱元素分布图和线扫描进行表征,如图4所示。图4a显示了R3区域δ铁素体相的明场图像,揭示了微观结构中δ铁素体的整体形貌和分布。环形高角度暗场图像提供了增强的对比度以识别元素偏析,见图4b。图4c中关键元素的分布图可以发现枝晶间δ铁素体中Cr富集和Ni贫化的情况,这意味着与马氏体基体相比,枝晶间区域的铬含量较高,导致高温下δ铁素体相的稳定范围更宽。图4d中的元素线分析显示了该区域特定线上各种元素的浓度分布。因此,在WAAM工艺过程中,在较高的冷却速度下,枝晶间区域不能充分奥氏体化,从而导致室温下δ铁素体的存在。相反,图4e-4h给出了残余γ奥氏体的形貌和元素分布,其中未检测到明显的偏析,元素Cr、Fe、Mn和Ni均匀分布在γ奥氏体和α'马氏体基体中。
.png)
图4. δ-铁素体相的元素分布:(a) BF图像、(b) HAADF图像、(c) EDS mapping和 (d) line analysis,以及 γ-奥氏体相的元素分布:(e) BF图像、(f) HAADF图像、(g) EDS mapping和 (h) line analysis。
(5)为分析双金属结构界面区域元素的扩散行为,沿构建方向逐层进行EDS线扫描。从图5a中可以发现,Ni元素浓度在ISR方向上呈现阶梯状下降趋势,从ASS侧到FSS侧有明显的过渡。相反,与Ni相比,Cr,Mn和Si元素的浓度变化相对平稳。舍弗勒图被广泛用于估计电弧焊后不锈钢的最终微观结构。根据图5a中双金属结构的元素分布,每一层的铬当量和镍当量坐标在舍弗勒图中用蓝色圆圈标记如图5b所示。ISR坐标精确定位在(A+M+F)相区内,与实验观察到的微观结构基本一致。此外,马氏体转变开始温度也是影响奥氏体稳定性的一个众所周知的因素。双金属结构沿构件方向的马氏体转变开始温度如图5c所示。很明显,在ASS区域马氏体转变开始温度始终低于室温,表明γ奥氏体可以在室温条件下保存而不发生马氏体相变。而界面区的马氏体转变开始温度则超过了室温。
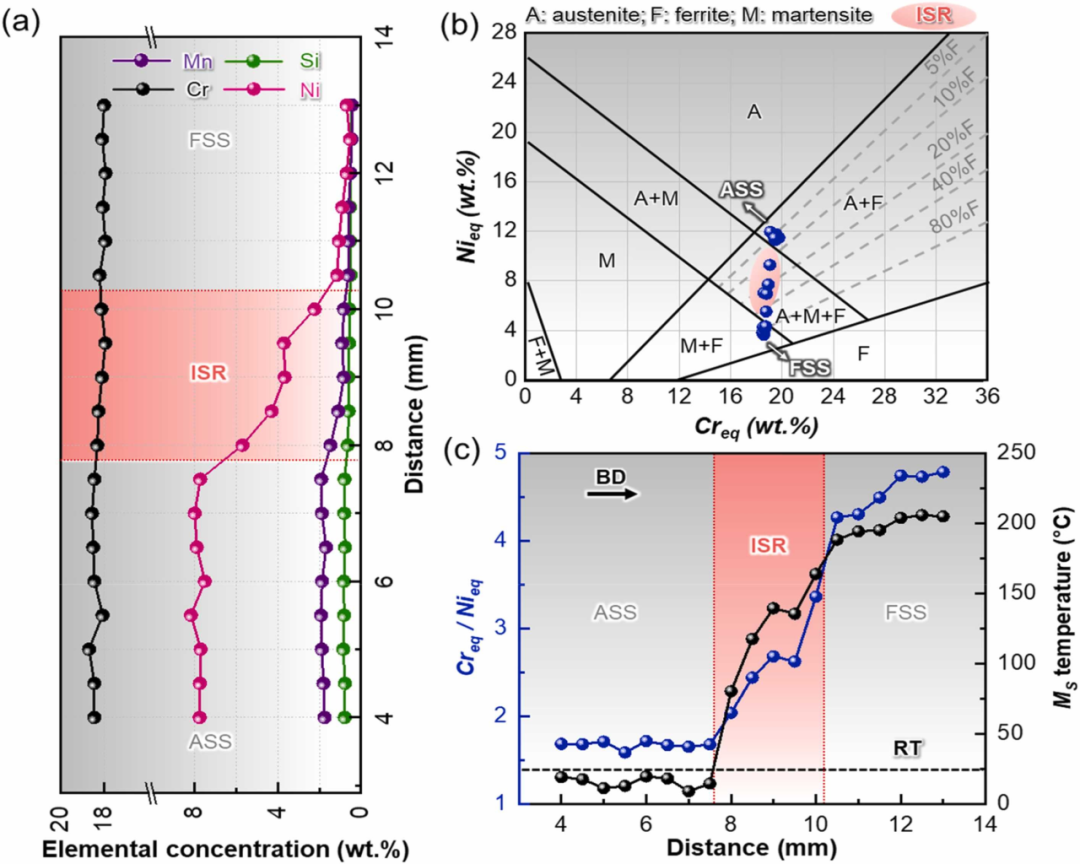
图5. (a) 双金属结构界面区域的元素分布,(b) 舍弗勒图 (c) 沿双金属结构构建方向的马氏体转变开始温度。
(6)一般来说,在电弧增材过程中,沉积层总是经历高频非稳态加热-冷却热循环,使相变顺序复杂化。这种复杂性使得通过实验观察增材制造部件的微观结构演变具有挑战性。为了解决这个问题,温度场模拟被视为并被用作一种有效的技术来协助研究沉积过程中的微观结构演变。作为决定界面区域微观结构演变的关键因素,R3的热历史详细给出,如图6a所示。R3中的热循环可分为五个阶段,每个阶段都代表不同的相变:熔化、重熔、部分奥氏体化、奥氏体化和淬火,如粉色方块所示。热循环曲线描述了R3的热物理参数,例如熔化温度、A3温度和A1温度。值得注意的是,道次间温度始终位于A1和Ms之间,表明在最后的淬火循环中形成了 α'-马氏体,而未经回火。总体而言,图 6b描述了R3的微观结构演变过程。如上图5c所示,当铬当量与镍当量比值大于2时,其凝固过程可判定为F模式,据此合理推断R3的相变顺序为:L → L + δ → δ → δ + γ → δ + α' + γ,最终反映为由α'-马氏体、δ-铁素体和γ-奥氏体组成的多相组织。
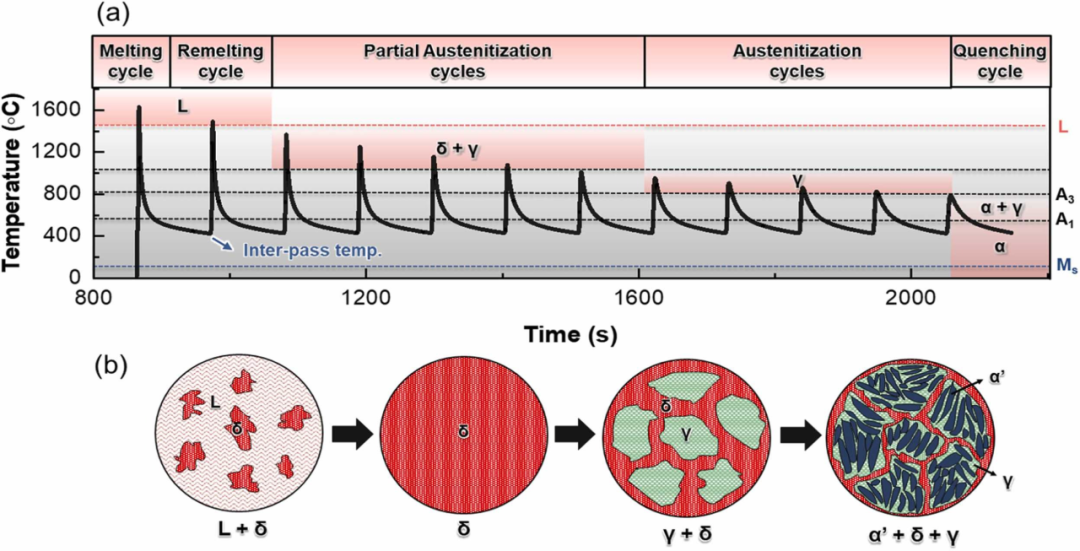
图6. (a) R3的热历史和 (b) 沉积过程中微观结构演变的相应示意图。
致谢
这项工作得到了日本科学技术振兴机构“下一代引领开创性研究”(JST SPRING)支持计划(No. JPMJSP2114)和日本学术振兴会(JSPS)“科研启动经费” (No. 24K22917)的资助。本文第一作者:徐一璞(日本東北大学 工学研究科材料系),本文通讯作者:王润梓(日本東北大学 材料科学高等研究所)。
本期小编 徐一璞(整理)
董乃健(发布)
|