引文格式:
Liu Z, He Z, Tu L, et al. A fatigue reliability assessment approach for wind turbine blades based on continuous time Bayesian network and FEA[J]. Quality and Reliability Engineering International, 2023, 39(5): 1603-1621.
Liu, Zheng, et al. "A fatigue reliability assessment approach for wind turbine blades based on continuous time Bayesian network and FEA." Quality and Reliability Engineering International 39.5 (2023): 1603-1621.
Liu, Z., He, Z., Tu, L., Liu, X., Liu, H., & Liang, J. (2023). A fatigue reliability assessment approach for wind turbine blades based on continuous time Bayesian network and FEA. Quality and Reliability Engineering International, 39(5), 1603-1621.
背景简介
由复合材料制成的风力涡轮机叶片(CWTB)会遇到疲劳失效问题。由于全面测试成本较高,因此采用有限元分析(FEA)来模拟CWTB的疲劳性能。为了考虑载荷和材料参数的相关失效和不确定性,本文提出了一种基于连续时间贝叶斯网络和有限元分析的疲劳可靠性评估方法。具体而言,通过有限元疲劳模拟确定CWTB各部件的危险区域,然后通过量化包括负载和材料参数在内的几个因素的不确定性来计算组件的失效概率分布。构建了CWTB疲劳可靠性的连续时间贝叶斯网络模型,通过与离散时间贝叶斯网络结果的对比分析,验证了该方法的有效性。
成果介绍
(1)在FEA中,输入参数包括载荷参数、材料参数等,上述参数的不确定性可以通过分布来量化。将随机生成的载荷参数、材料参数输入有限元模拟软件即可获得寿命数据。静力分析结果如图1所示,应力最大的危险区域位于剪力腹板与下壳的连接处,且靠近根部。同时,其他部件也有不同程度的损坏。疲劳分析结果如图2所示。可以看出,危险区域位于根部与剪力腹板的交接处,这与静力分析结果一致。同时,翼梁帽、根部、抗剪腹板、后缘、前缘和壳体中部均存在不同程度的损伤。为了进一步研究,在每个部件的危险区域选取几个危险点来代替整个部件来研究其疲劳寿命,对应的网格单元数分别为4235、48430、1576、59186、69936和21503。
.png)
图1 复合材料风电叶片静力分析结果
.png)
图2 复合材料风电叶片疲劳分析结果
(2)叶根是叶片与轮毂的连接部位,经常承受剪应力、拉应力的复杂组合、弯曲、扭转应力等,因而与其他部件相比其损伤最大。前缘和后缘是上、下壳体的粘接处,其不可避免的内部缺陷在循环载荷作用下扩展,形成裂纹萌生并导致渐进破坏。主梁由梁帽和抗剪腹板组成,是复合材料风电叶片的主要承载结构,随着使用时间的延长,主梁会发生损坏,复合材料风电叶片故障树如图3所示。
.png)
图3 复合材料风电叶片故障树
(3)在实际疲劳试验中,由于复杂的制造工艺、安装精度、外部环境、测量误差等,载荷、材料参数、叶片尺寸等都具有不同的随机不确定性。随机不确定性往往通过概率分布来量化,如正态分布、对数正态分布、Weibull分布、Gamma分布等。假设FEA中复合材料风电叶片的输入参数服从特定的概率分布,则可以确定分布参数,然后利用Matlab软件根据其概率分布生成不同的参数组合。将这些参数组合代入fe-safe,得到六个危险点的疲劳寿命,如图4所示。复合材料风电叶片的疲劳分析非常耗时,因此这里引入代理模型。基于有限元分析获得的原始数据,以有限元分析的输入参数为输入变量,以循环周期为输出变量,通过支持向量机(SVM)模型拟合载荷、材料参数等与疲劳寿命的隐函数关系。30组原始数据中,75%的原始数据作为训练样本,剩余的25%作为测试样本,检验SVM模型的预测精度。对上面提取的6个危险点分别应用SVM模型,预测结果以及FEA预测值与分析值的比较如图5所示。此外,每个危险点预测结果的最大误差如表1所示。从图5和表1可以看出,6个危险点中SVM模型与原始数据的最大误差为0.0155%,因此SVM模型可以用于数据扩展。然后,使用经过验证的SVM模型重新生成每个危险点的500组疲劳寿命数据。为了量化受随机载荷、不确定材料参数等影响的疲劳寿命的不确定性,采用不同的概率分布,如对数正态分布、Weibull分布和Gamma分布等来拟合再生数据。各危险点的拟合结果如图6所示,对应的函数参数如表2所示。
.png)
图4 六个危险点的原始疲劳寿命数据
.png)
图5 SVM 预测结果以及与 FEA 结果的比较
表1 各危险点预测结果的最大相对误差
.png)
.png)
图6 各危险点疲劳寿命的PDF曲线
表2 各危险点的PDF参数
.png)
(4)为每个危险点选择最合适的分布,通过 K-S 检验计算拟合优度 D,结果如表3所示。取显着性水平 = 0.05,样本量 n = 500,可以推导出D∞=0.0608。从表3中可以看出,各概率分布的D值均小于D∞,因此表2中的概率分布适合表征各危险点的疲劳寿命。而D值最小的概率分布通常被认为是最佳拟合分布,因此可以总结出对数正态分布,用来表征前缘、后缘、叶根、翼梁帽和叶片的疲劳寿命,而Gamma分布可以用来表征剪力腹板的疲劳寿命。确定的各危险点的概率分布及分布参数如表4所示,相应的失效概率函数曲线如图7所示。
表3 各概率密度函数的D值.png)
表4 确定的概率分布类型及其分布参数
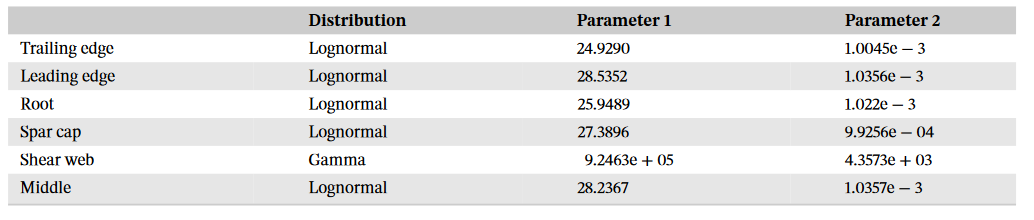
.png)
图7 叶片及其部件之间的故障概率比较
(5)将所研究的风电机组叶片的故障树转换为静态贝叶斯网络来推断系统失效概率,见图8。根据公式,计算的系统故障概率曲线如图9所示。复合材料风电叶片的设计要求是其疲劳寿命不低于2×106次循环,相当于20年的使用寿命。由图10可知,当N=2×106时,失效概率接近于0,因此所研究的复合材料风电叶片满足设计要求。
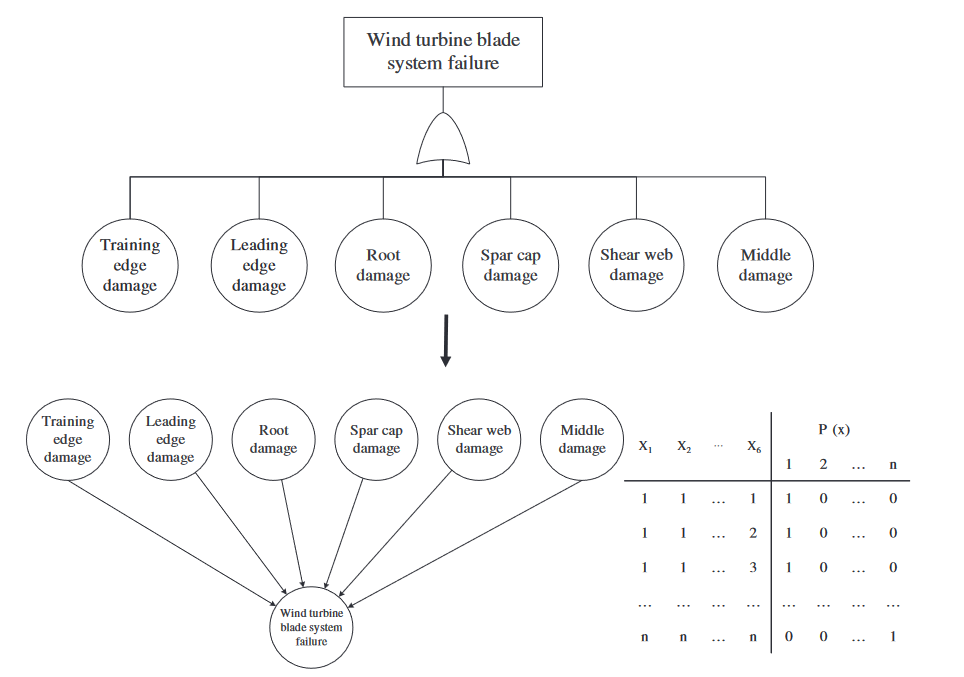
图8 FT 到 BN 的转换
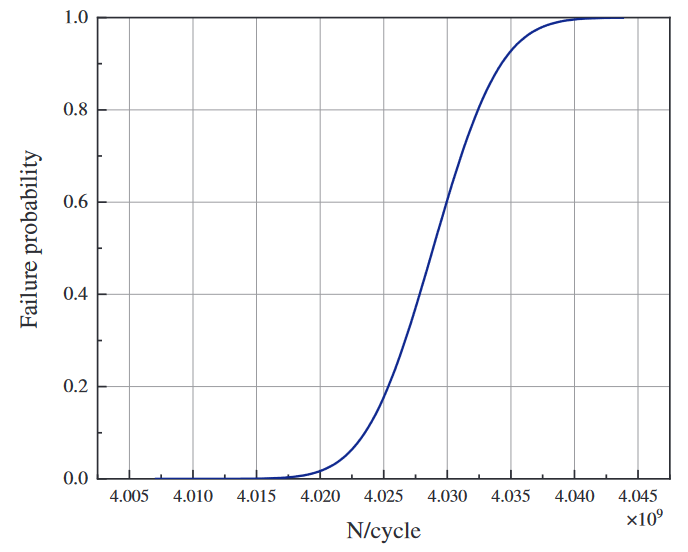
图9 所研究叶片的系统失效概率
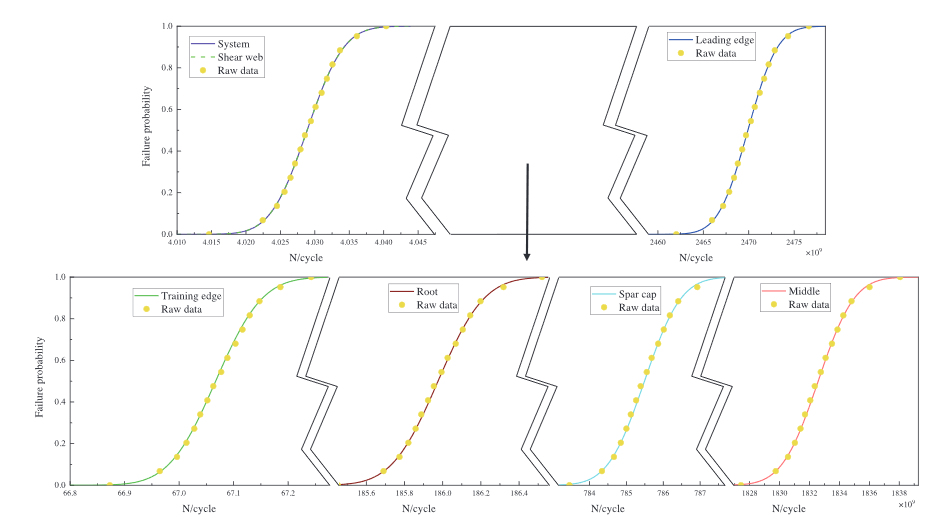
图10 叶片及其部件之间的故障概率比较
致谢
该研究得到了国家自然科学基金(51905116)、国家自然科学基金(52175132)、广东省基础与应用基础研究基金(2020A1515111141)和广东省哲学社会科学“十三五”青年项目(GD20YYS03)的资助支持。本文第一作者:Zheng Liu(Guangzhou University),通讯作者:Xin Liu( Guangzhou University)。
本期小编: 石 韬(整理)
姚辰霖(校对)
王康康(审核)
王永杰(发布)
|